RAYNOK PROJECT CASE STUDY
The Lindemann Performing Arts Center
The Lindemann Performing Arts Center is a flexible arts space that has been designed to influence young artists to create within a space that they can shape.
The room features glass walls that look out onto the surrounding cityscape and campus of Brown University from within the auditorium and performance space allowing for natural light to fill the room. Above the glass sits 5 movable gantry systems powered by Serapid chain technologies that move in and out to change the size of the room and create a wide open or intimate performance space.
High above and covering the entire performance area are 16 smooth round surfaced acoustic reflector panels that can be raised, lowered, and tilted in the X and Y axis to “tune the room” for the perfect sound whether it is acoustic or amplified.
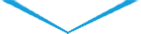
Project Information
Project: The Lindemann Performing Arts Center
Owner: Browns University
Location: Providence, Rhode Island
Completion: Date: September 2023
Project Partner: Texas Scenic Company
Architect: REX NY
Theatre Consultants: Theatre Project Consultants
Type of Venue:
Performing Arts Centre with variable configurations
Room can be transformed into a thrust stage, theatre in-the-round, concert, proscenium, or flat floor
Hardware included:
-
Stage lifts by Gala Systems
-
A Gala lift system with storable seating that allows the room to be converted to an event space
-
16 multi-axis Acoustic Reflector Panels
-
5 seating gantries that weigh over 5-ton each and move in and out of the space to reconfigure the room
-
Multiple point hoists for raising and lowering scenic elements
-
16 chain hoists for raising and lowering lighting trusses and speaker clusters
-
Blackout curtains that cover the glass walls to block out the light
-
3 manually maneuvered light bridges
-
A motorized choral platform
Project Challenges
The main challenge of this project were aspects of life safety and protection of public and personnel when the room is in process of reconfiguration.
The five seating gantries include two technical levels above the two public levels. Moving each gantry creates a fall hazard at all four of those levels at each end of the gantry. Further, below each of the public levels are sheets of glass suspended from the underside of the gantry hung just 12mm above the surface of the floor.
High above the playing and seating areas are 16 multi-axis acoustic reflector panels, and above them building fire suppression system. The challenge here was to ensure unrestricted disbursement of fire suppression in the event that a fire occurred.
Moving the room, in the manner that it can be moved, alters the air flow and affects the usage of the HVAC system especially when the south gantry is moved to its full in position to the north. This required the HVAC building controls to aware of the room configuration so that air flow could be adjusted for guest comfort.
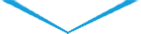
Inside the Performing Arts Center
16 Multi-Axis Acoustic Refector Panels
One of the key features of the architectural design of the Lindemann is the requirement for adjusting between the needs of acoustic sound, amplified sound, spoken word, and control of reflected sound in a banquet setting.
These Acoustic Reflector Panels had to be moved into the building before it was closed in. They also need to move in an automated fashion should the sprinkler system be activated. It takes 48 hoists to move these units and only 90 seconds to put them into emergency mode on sprinkler activation.
Creating A Flexible Arts Space
The Raynok operator at Lindemann uses a pre-visualizer to look at the arrangement of the ARPs before sending the command. Raynok provides the operator with a view of the starting point, the motion path, and the ending point of each element. Motion can be witness to see conflict before execution in Raynok’s offline editor.
Project Solutions
The first group of hazards we noticed on this project were related to the risks of falls and pinch points when changing the configuration of the room. To resolve and protect against these hazards a series of lockable doors, gates, and railings were installed. The machinery control system was in command of locking and monitoring the network of fall prevention locks.
Further to the locking rails it was noted that the manually moved lighting bridges had to be in known positions before moving the gantries or reflector panels. An additional series of sensors were added to ensure proper positioning and the safety of personnel.
Protection of the glass from collision with an immovable, or even small, object became very important. The challenge was to ensure that the floor was clear and clean and that nothing would encroach on the 12mm air gap between the floor and the bottom of the glass. To address this an inspection procedure was written and to ensure that procedure was followed the concept of a security warden was employed. The process of securing a building can require a security officer to walk around the building and check the status of doors, windows, stairwells, etc.
Throughout their walk warden stations are strategically placed that require the officer to “check-in”, noting the time of passing through the area. This concept was employed using a series of RFID tag readers. The technician walks the room and ensures that there are no obstructions of personnel in the hazard zone. The machinery control system monitors the cards and once all have been tapped a window of time is opened to allow the gantry systems to be moved.
Fire suppression is a paramount concern in any building. In this room the suppression sprinklers were covered by the acoustic reflector panels. Two problems were created here. One is that the sprinkler water would not be able to reach the floor if blocked by the reflectors and the other was that the reflectors themselves could fill with water and become a hazard should the water overload the suspension system. The life safety officer’s requirement was for a fully automated move of the panels without human intervention with the control system and the support of a backup generator.
The solution employed involved overriding the Emergency Stop and hold-to-run systems, monitoring the status of backup power, and executing moves that would not overload the backup power system. Further, if the signal to execute the fire sequence was erroneously sent the Emergency Stop System had to respond to an intervening command to stop from one of the E-Stop button stations. The number of error checks that must be completed in less than a second is astounding.
The Lindemann Build Gallery
Here is a Lightbox Gallery of images that were taken during the build of this fabulous facility. Click on any image to open the Gallery and click off the image to close the Lightbox.
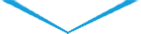
Trust Raynok to Manifest the Vision.
Automation of Rigging and Concert Trussing
Flying, Travelling, and Tracking Video Walls
Moving Curtains and Acoustics
Architectural Equipment – Architainment
Position Monitoring and Real Time feedback
Complex and Synchronized Motion
Performer and Stunt Flying
Stage Lifts, Turntables, Wagons, and Floor Machinery
Wireless Motion Control
Shared Position Data for Video, Lighting, and Audio tracks
Safe, Reliable, Repeatable and Precise
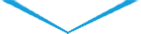